1. Introduce of stone bridge cutting machine
2. Features and applications of bridge cutting machine
3. What are the most common types of stones cut with these machines?
4. Machine Details
5. Stone bridge cutting machine specifications
Introduce of stone bridge cutting machine
Stone bridge cutting machines are specialized equipment used to cut stones for construction of bridges, architectural structures and monuments. These machines utilize diamond blades and abrasive wheels to achieve high precision cuts in granite, marble and other hard stones. Stone bridge cutting machine is a high-automatic machine for cutting marble, granite and high-value slab processing. The main beam of this machine can moving through PLC control makes machine working accurate. This stone bridge cutting machine controled through computer program with high accurate, automatic, easy-operated and stable performance. We use high quality steel materials to make sure bridge cutting machine has a long?service time and powerful cutting. All components are imported from oversea and famous brand in china. Also you can choose the combine-joined bridge cutting machine which is easy to remove and install. The gears and bearing are purchased from high quality brand. Also, we test all spare parts before we using them so that we can guarantee the quality of bridge cutting machine.
Features and applications of bridge cutting machine
Stone bridge cutting machines come with multiple features to enable accurate and efficient cutting of stones. They are built with a sturdy frame and bridge to provide a stable platform for stone cutting. The machines offer multiple spindle options to hold and rotate circular diamond blades and grindstones at different speeds. The spindles can move in multiple axes to achieve angled and beveled cuts. Some machines also have hydraulic clamps to firmly secure the stones during cutting. The machines also have cooling mechanisms to prevent overheating of the stones.
Stone bridge cutting machines find applications in cutting stones for the construction of stone bridges, cladding of bridge pillars and abutments, architectural facades, monuments, sculptures, etc. The most common applications of these machines are:
Specific Cutting
1. Cutting stones to specific dimensions, shapes and textures for use in stone bridge construction and cladding. These machines can achieve precise cuts and finishes as required for structural bridge elements as well as decorative features.
Customized Cutting
2. Cutting customized 3D shapes, sculptures and patterns in a wide range of hard stones. These machines offer multi-axis cutting capabilities to produce unique architectural forms and artwork.
High Volume Production
3. High volume production cutting of pavers, cobblestones, tiles and slabs used in civil construction projects. Automatic stone cutting machines with multiple blades and spindles are well suited for such high production applications.
Bridge Cutting Machine Diamond Blades
4. The diamond blades and grindstones on these machines come in a range of grit sizes, diameters and bond types to suit different stone cutting applications. The diamonds and abrasives cut through the hard stones through a combination of sawing, grinding and polishing actions.
Automated Tool Changing
5. Some machines are equipped with automated tool changing mechanisms to facilitate quick changes between different diamond blades, wheels and other attachments. This helps optimize the machines for high production cutting of varied stone profiles and sizes.
CNC Controled
6. Advanced machines incorporate CNC controls, servo motors and precision linear guides to enable complex 2D and 3D cutting operations. 3 or more axis of motion can be computer-controlled for intricate stone carving and shaping. Some machines also have options for laser guides and digital readouts to achieve high precision cuts.
Power of Bridge Cutting Machine
7. Bridge cutting machines require a significant amount of power to operate which is supplied through heavy-duty motors. Most machines use electric power, but some are also diesel or gasoline powered for non-electric worksites. Hydraulic circuits are also needed to apply pressure for tightening clamps and other functions.
Ergonomic Controls
8. A well-designed stone cutting machine provides ergonomic controls for the operator. This includes adjustable stations, joystick or touchscreen controls, clearly marked functions and emergency stop buttons. Since stone cutting involves flying rock debris, the machines are also equipped with protective shields and the work area needs proper dust control mechanisms.
What are the most common types of stones cut with these machines?
The most common types of stones cut using stone bridge cutting machines are:
• Granite –
Granite is an extremely hard igneous rock that is commonly used in bridge construction and building facades. Granite can withstand immense loads and environmental stresses, making it ideal for bridges. Stone cutting machines are able to achieve smooth and polished cuts in granite with diamond blades and abrasives.
• Marble –
Marble is a metamorphic rock that is valued for its strength and beauty. Marble blocks are cut into decorative elements for bridges, monuments and buildings. Marble cutting requires the use of diamond-tipped blades and water-cooled equipment to prevent overheating.
• Limestone –
Limestone is a sedimentary rock commonly used in bridge abutments, retaining walls, edging and cladding. Limestone is abrasive in nature, so the stone cutting machines require frequent diamond blade changes to achieve clean cuts. Limestone also benefits from water-cooled cutting to minimize dust.
• Sandstone –
Sandstone is a sedimentary rock used in architectural elements such as archways, window sills, and wall cladding. Sandstone can have varying hardness depending on its composition, so blade selection is important for optimal cutting. Sandstone also requires dust control methods like wet cutting.
• Slate –
Slate is a fine-grained metamorphic rock suitable for flooring, roofing, pavers and tiles. Slate cutting machines use diamond blades and grindstones to cut slate into sheets, strips and custom profiles. Water cooling and vacuums help manage slate dust which can be flaky.
• Quartz –
Quartzite is an extremely hard metamorphic rock used in countertops, flooring and architectural panels. Quartzite cutting machines require the use of high quality diamond blades and abrasives to achieve precise cutting edges. Cooling fluids and dust extraction are essential for quartzite cutting.
So the most common stones for cutting with bridge cutting machines are granite, marble, limestone, sandstone, slate and quartzite. These machines are able to cut and finish these hard stones with proper tooling and dust control methods. The choice of stone depends on the specific applications in bridges, buildings or monuments.
In summary, stone cutting machines are essential equipment for shaping hard stones used in major infrastructure and construction projects. They help achieve the precision, efficiency and high productivity needed for cutting stone bridge elements and other architectural features. These specialized machines continue to evolve with more advanced automation and tooling options for cutting challenging stone materials.


Machine Details




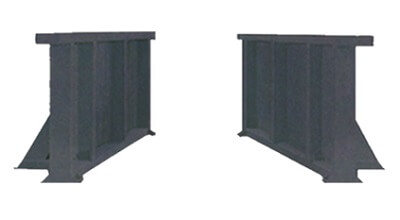



Stone bridge cutting machine specifications
Name | Unit | Value |
---|---|---|
Blade diameter | mm | 300-400 |
Blade quantity | n | 1 |
Power of main motor | kw | 11 |
Total power | kw | 15.95 |
Range of horizontal and lengthways | mm | 3200 |
Range of lifting | mm | 300 |
Size of worktable | mm | 3000*1950 |
Rotation angle of worktable | n° | 360 |
Overturning angle of worktable | n° | 85 |
Size of the machine | mm | 6000*5000*2800 |
Weight of the machine | t | 5.8 |